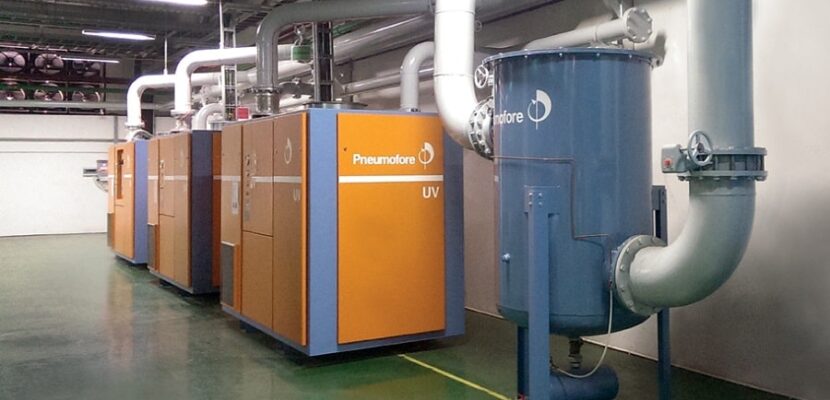
The Vital Components Needed in Your Vacuum Systems
- Mark Edwards ·
- 0 Comments ·
- July 25, 2021
When it comes to operating a vacuum, you are only as good as the components you use. You need to make sure the system is expertly constructed so that it works as effectively as possible, and that is something we are going to look at below.
There are a lot of components that are required by an ultra-high vacuum system, including a 3 way solenoid valve, and this is especially the case if an object within the chamber needs to be manipulated in any way. One of the problems with manipulating objects within vacuum chambers is ensuring that the low pressure is maintained and that the external environment does not enter the system.
There are a number of ways in which mechanical transmission can be achieved within a UHV system. These methods are split into two major groups: those for manipulating objects over small distances or low speeds; and those needed for larger movements or that involve high speeds or high torque.
The first group can be served by O-ring seals. While these seals provide a low leak rate, they do have the drawback of not always being bakeable. Care, therefore, needs to be taken when choosing seals for use in ultra-high vacuum environments. One way to improve their usage range is to use Viton A O-rings that are lubricated with graphite. A possibly more cost-effective alternative is to use flexible bellows. These would be manipulated for outside the vacuum with feedthrough, fitted with a suitable flange, being used to connect the internal and external parts. The bellows system does not work as effectively with the second group.
One solution for your business here is to employ the use of a magnetic or electromagnetic coupling. For example, the coil of an electric motor is placed outside of the vacuum, with the rotor placed inside to provide rotary motion. It is important that these ultra-high vacuum parts do not become sources of gas and must therefore be made from suitable bakeable materials, and of minimum possible size.
Bakeable Conditions of Components
UHV heater appliances for baking ultra-high vacuums are widely available and differ in shape, size and manufacturing detail. One thing they all have in common is the ability to raise the heat inside the vacuum components enough to remove moisture and lower degassing rates from the ultra-high vacuum system and joins.
The use of baking for this purpose affects the choice of ultra-high vacuum parts that you source. All parts from the chamber to the flanges and O-rings, and of course the UHV pump itself, need to be suitable to undergo this process. If UHV accessories are not compatible with baking, then they either need to be shielded during the process or removed. Removal of parts is not ideal as it increases the risk of contaminants entering the system. Shielding is a possibility, but affects the baking technology involved and can be time-consuming as well as difficult. It is much more time- and cost-effective to source components and technology that are designed to undergo the baking process.
When choosing an ultra-high vacuum supplier for your products, look specifically for bakeability; and for the temperatures that the part can withstand. Baking usually occurs at temperatures between 200oC and 450oC, so a minimum temperature requirement for your parts needs to be 200oC. If this information is not present, it is best to investigate further rather than taking a risk. Baking parts that are not manufactured to withstand the temperature could have catastrophic effects on both the individual part and the vacuum process as a whole.